Print. Laminate. Cut. Done! Sounds simple, right? But producing a laminated digital piece isn’t as simple as it seems. Once artwork has been printed, a print shop has to wait 24 to 48 hours to laminate the piece. Material cannot be taken off the printer and laminated immediately because the final laminated piece might not look the way it was intended:
- Ink could bleed or blotch.
- There may be bubbles in the laminate, also called “silvering,” which gives the piece a hazy appearance. Silvering can also give the piece a texture similar to an orange peel or the illusion of silver reflective lines.
- The lamination may not stay in place. “Delamination,” or the separation of layers within a print, occurs when lamination is applied too soon after printing and can’t fully adhere to the materials. This can happen either throughout the piece or near the edge, called “edge lift.”
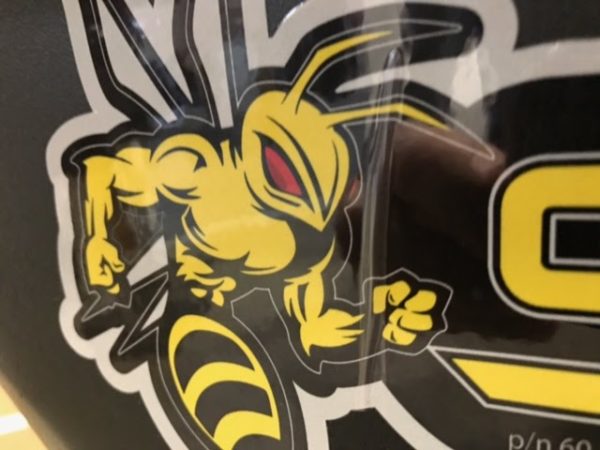
An example of delamination within the center of a print.
The main reason for these defects is outgassing or, more specifically, a lack thereof. Outgassing is the release of trapped gas from a solid. Ink penetrates the surface of the printed material, and its pigment resin remains as the ink color while the solvents dissolve, or outgas.
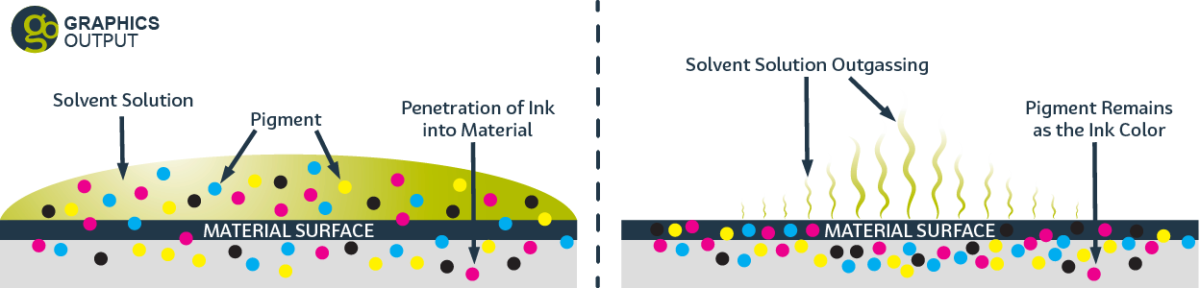
A cross-section of solvent ink on a surface before and after curing.
Some in the printing industry think outgassing is a myth and that the waiting period isn’t needed. The truth is that the amount of time needed to outgas depends on a variety of factors. Sometimes, outgassing doesn’t require a full 24 hours. The main factors that determine the amount of time needed for outgassing include the type of ink used, the amount of ink used, and the materials used.
Type of ink used
Solvent inks and eco-solvent inks both are waterproof, scratch-resistant, fade-proof, and low-cost; however, there are other factors to consider when selecting the best option for your printing process.
Traditional solvent inks have a stronger chemical makeup, which means they will dry faster and penetrate deeper into a wider variety of media that doesn’t necessarily need to be print-treated or coated. Many traditional solvent presses “flash off” solvent gasses as they print, meaning they use heat to speed up evaporation times. These durable inks can resist fading for up to seven years without lamination. However, the solvent chemical evaporating from the print can cause hazardous fumes, known as volatile organic compounds (VOCs). Proper ventilation, space, and disposal are required for this type of ink.
Eco-solvent inks, by comparison, have a lower hazard level for humans. These odorless inks are not as aggressive as traditional solvent inks, and eco-solvent inks are usually derived from mineral oil. That means this option is better suited for indoor environments without special air ventilation. This option also has a wider variety of drying times than traditional solvent inks, taking anywhere from a few seconds to 12 hours. The tradeoffs include eco-solvent inks not being as compatible with as many printed materials as traditional solvent inks, less durability, especially against alcohol and other cleaning solutions, and a higher likelihood of fading within three years without lamination.
While eco-solvent inks are not as harsh as traditional solvent inks, both use solvents that are corrosive to print substrates and adhesives. This means that most ink manufacturers recommend waiting 24 hours before laminating for all solvent prints to avoid print failure.
Amount of ink used
The more ink coverage on a piece, the more time needed to outgas. This includes both the square inch area of material covered by ink and dots per inch, or DPI. The higher the DPI, the darker the ink will appear and the more time required for outgassing. Using a solid, full-coverage coat of rich black on a piece, for example, should take the most time possible to outgas. This is because every square inch of material would be covered in ink, and rich black uses a lot of ink per square inch.
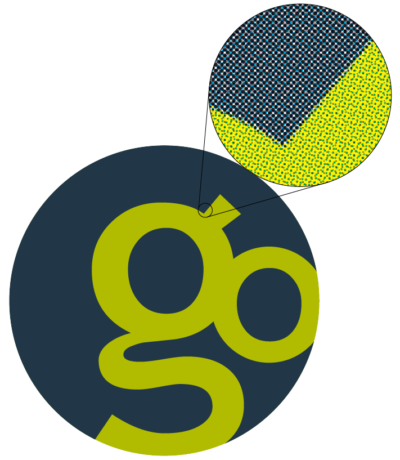
CMYK printing uses four inks: cyan, magenta, yellow and key, or black.
When the four colors are combined by printing small dots of each color, the human eye sees the final compound image and color.
Materials used
Polyester and polycarbonate laminations are very chemical resistant, so they do not allow for much outgassing to occur through them. By comparison, vinyl lamination is easier for solvent gasses to pass through, allowing outgassing to continue even after lamination has been applied. This means that prints with a vinyl overlaminate can be laminated after a shorter outgas time.
Proper outgassing also becomes more important when the part being produced is a window decal that needs visual clarity, such as a perforated vinyl decal on a car window. Since window visibility is already being diminished, lamination clarity is extremely important. Allowing window vinyl to outgas for as long as possible before laminating will reduce the opportunity for outgas-caused haziness.
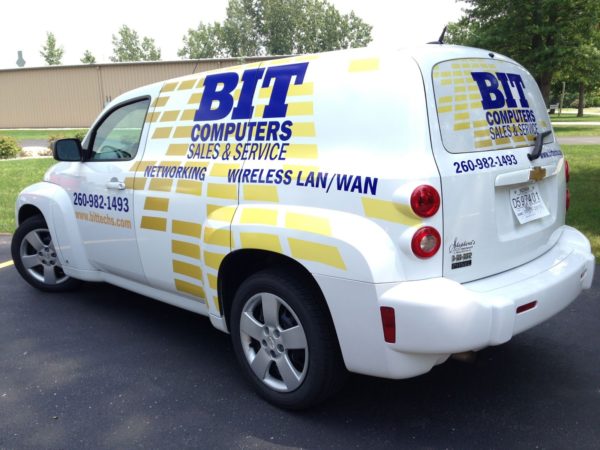
A vehicle window wrapped with perforated window vinyl needs to be as optically clear as possible to keep the driver safe.
Need a project digitally printed and want to assure your laminate looks perfect, without any outgassing issues? Graphics Output is proud to produce high-quality parts daily. Request a quote online, shoot us an email, or call 260-748-0577.