Myth-busting isn’t just for two guys with goatees on network television, so forget what you’ve been told—especially when it comes to these 10 common myths from the graphics and printing industry. You may be surprised to learn a few new, and hopefully helpful, facts.
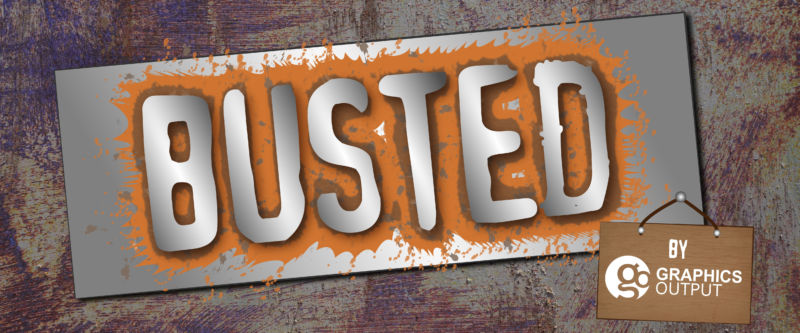
1. Decals are only for cars/walls/windows/etc.
Graphics can be made for virtually any surface, but the way they are made will change depending on the application. For example, a warning label for a piece of painted machinery will require a different material build than a window decal for your business, which will also be different from that Live, Laugh, Love decal on your mom’s living room wall.
2. Vinyl is vinyl, polycarb is polycarb, polyester is polyester…
Cast vinyl vs calendered, hard-coated or not, thickness, finishes, and rigidity all determine the best material for your application. Plus, two items made of the same material can be drastically different. For example, is it smooth and tissue-paper thin? Or thicker with some texture? For more clarification, check out our cast vs. calendered vinyl or our polyester vs. polycarbonate posts.
3. When in doubt, use a thicker adhesive
Thicker adhesives applied to a smooth surface will ooze, causing dirt to accumulate around the decal and shorten its service life. Instead, save the thicker adhesives for textured substrates, where the excess adhesive will sink down into the surface grooves of the material.
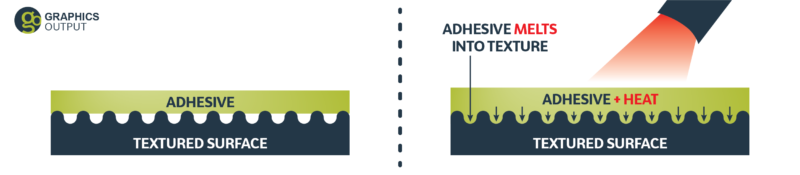
4. The stickier an adhesive feels, the better it will adhere
Some stronger adhesives have less initial tack but develop a strong bond over time. Unsure which adhesive to use? Look at its technical specifications—what’s its peel? its shear?—to determine if it will stick to your substrate.
5. Application temperature is the same as service temperature
Application temperature is the temperature range that your decal can be successfully applied. Most adhesives will not bond well in cold environments or to cold surfaces. The service temperature, meanwhile, is the range that your decal can go on living its best life without failure, which is almost certainly a larger range than the application temperature. For example, General Formulation’s standard 201 white permanent vinyl can only be applied if the ambient temperature is over 40 degrees Fahrenheit, but its service temperature ranges from -40 degrees Fahrenheit to 180 degrees Fahrenheit.
6. Decals and wraps will damage your paint
Most wrap vinyl is designed to be removed down the road and protect your paint during its lifespan. Follow the proper installation and removal procedures for your specific material, and you’ll be golden.
7. Application tape removal is done immediately after applying a pre-spaced decal
Not allowing your decal some time to adhere (aka dwell time, usually two to three minutes) before attempting to remove its premask can cause adhesion to fail. When the premask tape’s bond to the top of the decal is stronger than the decal’s bond to the application surface, your decal will peel up with the premask, sometimes ripping the vinyl and ruining your decal. So apply the graphic, give it some time to bond with its new bestie, and then come back in a few minutes to remove the premask tape.
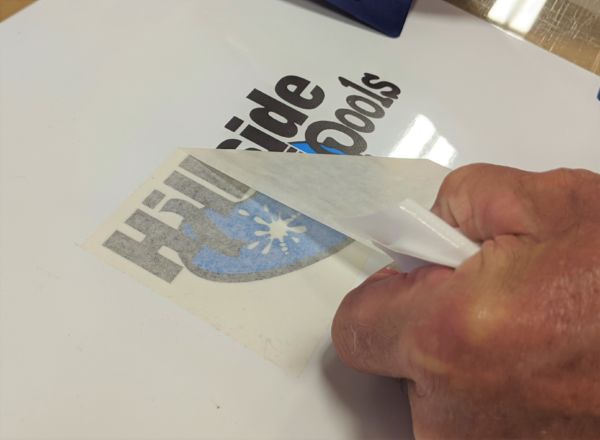
8. Outgassing isn’t ever necessary
For UV cured and eco-solvent inks, which are both becoming more popular in digital printing, outgassing isn’t needed before further processing and finishing. But traditional solvent inks still need 24 to 48 hours of time to outgas to prevent silvering, delamination, and shrinking and curling after cutting. Skip this step at your own peril.
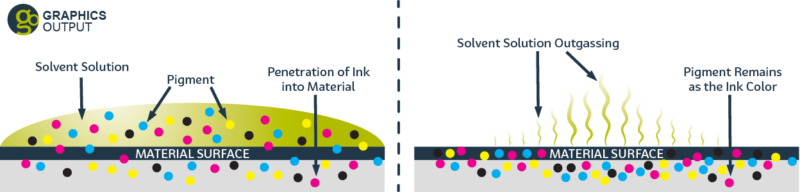
9. Wind slits help make banners more stable in the wind
Cutting slits in your banner only makes it more likely to rip and doesn’t help much as far as wind goes, according to The Conversation, a news organization funded by Queensland University of Technology and the University of Queensland in Australia. The best ways to reduce wind load on a banner are to use a smaller banner, switch over to a mesh material, or cut a series of round holes (not slits or flaps) into the vinyl, essentially turning it into Swiss cheese. We don’t recommend that last one, even if it is “effective for reducing wind load.”
10. Pantone Matching System (PMS) colors can be simulated with CMYK
For this, we turned to Pantone itself, which states on its website that PMS spot colors will be cleaner and brighter than if they were created via CMYK. Plus, many spot colors are outside the possible CMYK color gamut, so substituting CMYK for PMS will result in a different color. Even though Pantone created an entire color guide book just for converting from PMS spot colors to CMYK colors, , the results aren’t always great—or even within tolerance of the original spot color.
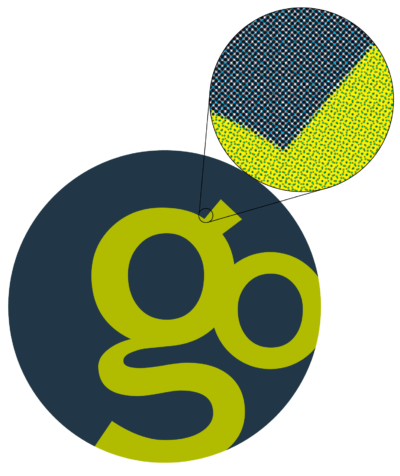
A closer look at an image created with the four-color, or CMYK, process. CMYK printing uses four inks: cyan, magenta, yellow, and key (or black). When the four colors are combined by printing small dots of each color, the human eye sees the final compound image and color.
Feeling smarter? Go ahead and share this post with your friends so they can feel smarter, too. Have some questions, or maybe know another printing myth that should be debunked on our blog? Shoot us an email and get the conversation started. We’d love to hear from you.