When purchasing a graphic for something like a vehicle wrap, control panel overlay, or warning label, one of the last things to consider is the graphic’s finish. To choose the correct materials, your priorities matter: Do you need a clear finish? One that’s easy-to-clean? Something scuff-resistant?
There are three primary finish options: gloss, matte, and semi-gloss.
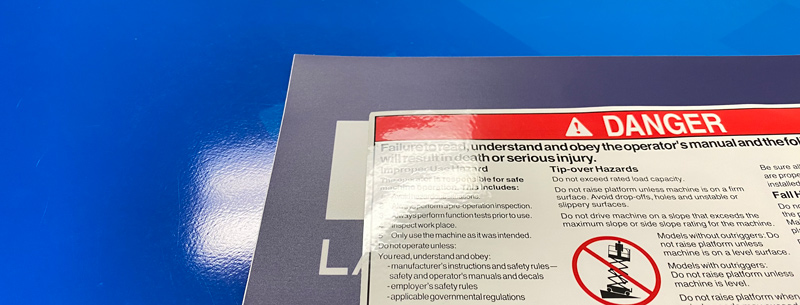
From left to right: lustre, matte, and gloss.
Finishes
Gloss
Gloss and high-gloss finishes are the most common lamination types for flexible graphics such as cut vinyl decals and warning labels. This is because gloss finishes are the most transparent, allowing for better art clarity and color vibrancy. Gloss finishes are typically very smooth and easy to wipe clean. Because they are the most common, they also are the most economical. Unfortunately, gloss finishes also have high glare, which reflects light and can make material difficult to read.
Matte
Matte finishes are great for softening images and reducing glare. They are often used in outdoor applications such as aluminum signs, which would be hard to read with too much glare.
Semi-Gloss
Also referred to as a luster or satin finish, semi-glosses combine the best of gloss and matte finishes. With light reflection levels between the two, a semi-gloss finish reduces glare without muting colors. However, semi-gloss finishes are sometimes unavailable, as with textured polycarbonate films.
Pros | Cons | |
Gloss |
|
|
Matte |
|
|
Semi-gloss |
|
|
Textures
Adding texture to your lamination or choosing a textured substrate can increase abrasion-resistance and reduce glare. In most cases, however, they also change the color of the overlays, unless you select a smooth texture.
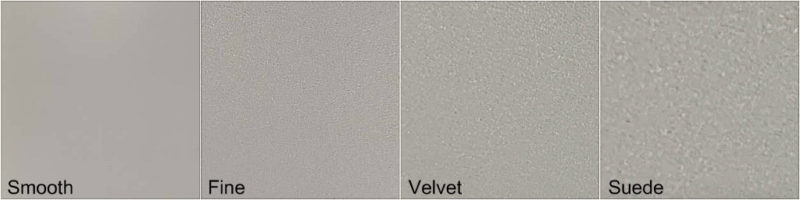
A close-up of textured polycarbonate shows the various levels of textures.
Smooth
Smooth textures are the clearest because there is no grain or pebbling to distort the image in any way. A smooth gloss will be completely transparent, whereas a smooth matte is only translucent. Because of this texture’s clarity, imperfections or dirt in or on the print will be visible, and LED light diffusion is usually impossible. Materials with a smooth texture are easy to wipe clean but will offer little to no scuff resistance. Smooth is the most common texture for flexible substrates, making it the most economical for most applications.
Fine
Fine textures offer some scuff resistance and LED light diffusion, and they are still fairly easy to clean. Because the pebbles in fine textures are small and offer less protection than textures with larger pebbles, polycarbonates with a fine texture have a shorter lifespan than those with larger textures. They are more likely to wear smooth with repeated use.
Velvet
Velvet textures offer plenty of scuff resistance and LED light diffusion. It’s by no means bumpy, but there is a slight grain. Dirt can stick inside the texture’s grooves, making this material difficult to clean. Velvet is the most common texture for polycarbonate graphic overlays.
Suede
Suede textures offer excellent scuff resistance and LED light diffusion and are usually used only when one or both of those characteristics are needed. It is the most textured, least smooth option and feels like a very fine, soft sandpaper. Dirt can stick inside the texture’s grooves, making it difficult to clean. A suede texture makes small text difficult to read.
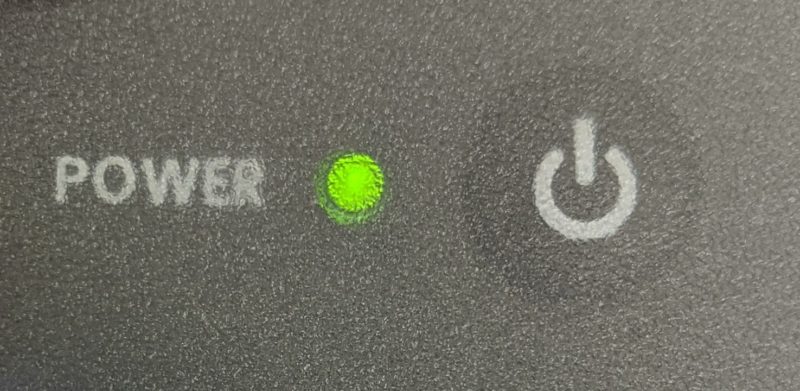
Suede texture offers the highest light diffusion for LEDs.
Other/Embossed Options
Other textures are available for different applications. For example, a wall vinyl may have a woven or fabric-like texture to mimic the look of wallpaper. A brushed texture on rigid polycarbonate can give the appearance of brushed metal, ideal for an application where brushed metal would not hold up well, such as a floor graphic or phone case. Because these offerings are not widely used, pricing can be high.
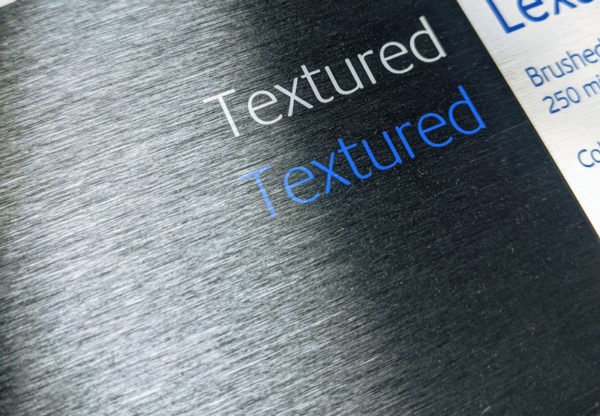
A polycarbonate film with brushed texture can simulate brushed aluminum and add durability.
Pros | Cons | |
Smooth |
|
|
Fine |
|
|
Velvet |
|
|
Suede |
|
|
Other/ Embossed |
|
|
Combining Finishes and Textures
Print items have both a texture and a finish. Often the texture is applied to one side of the substrate, side A, and the finish is on the other, side B. If no texture is specified, the default finish is smooth.
Two of the most common polycarbonate films for graphic overlays are 8A35 Lexan and 8B35 Lexan, each with velvet texture on side A. However, 8A35 has a polished side B, and 8B35 has a matte side B. As a result, 8A35 is much shinier and clearer, with more vibrant colors. 8B35 is hazier and duller, which can mask scratches.
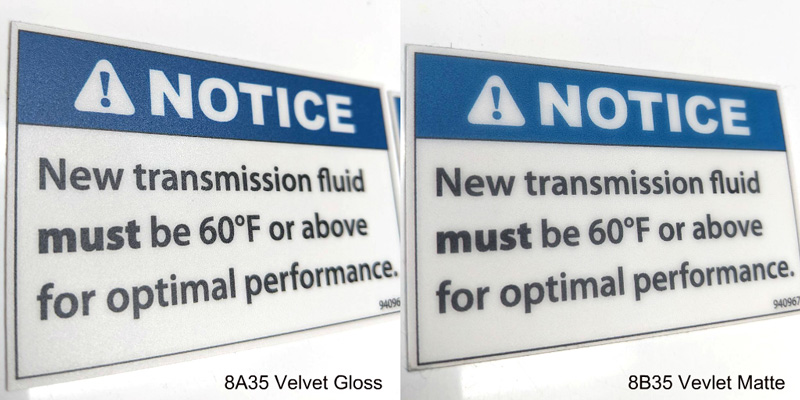
If you’re unsure which texture or finish is right for your application, Graphics Output is happy to provide samples and review options to find the best fit. Email sales@gographicsoutput.com, call 260-748-0577. or request a quote online.