Why should I define Quality Control standards?
Things get dirty, accidents happen, and nothing is 100% flawless. That applies to your vendors’ processes, too. So how do you define acceptable quality?
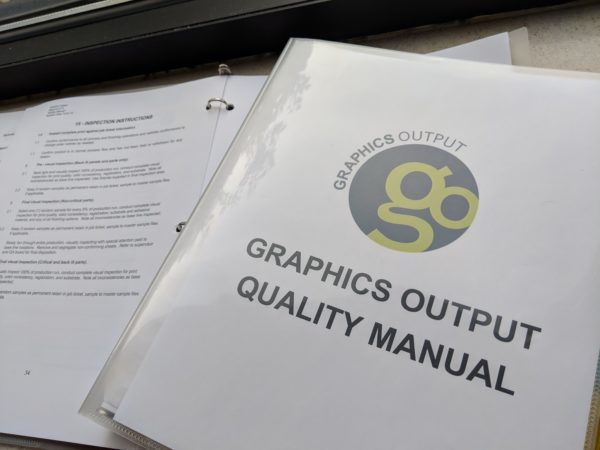
The Graphics Output Quality Manual, which is reviewed and updated annually.
Many suppliers like Graphics Output invest in programs like Six Sigma, LEAN 5S, or ISO to reduce spoilage and improve quality control. Still, some parts can come through production with minor defects. Knowing what defects are acceptable will help both your team and your graphic supplier’s team.
On one hand, your standards should be strict enough that end users won’t see flaws in your product. On the other hand, quality control time can be expensive, and standards that are too strict can cause your decal prices and lead time to increase. The worst case scenario is when standards aren’t defined at all. That’s when you’re more likely to see defective parts or have trouble rejecting parts that meet your supplier’s internal guidelines. Defining acceptable and unacceptable defects provides objective guidelines, saving time for you and your supplier.
For the sake of this blog, we’ll share quality control issues from the kind of work Graphics Output does as a commercial printer. The overarching issues can easily transfer to other industries.
Types of Defects
Decals and graphics can have many different types of defects that may or may not be acceptable. For example, a backlit overlay with a pinhole of missing ink is often defined as unacceptable, as light will pass through the hole noticeably when the backlight is on. But if the pinhole of missing black ink is on a decal on a black metal surface, you wouldn’t notice and it wouldn’t affect the use or lifespan of the overlay.
Consider the application and use of the decal when defining criteria for defects. Specifics about dust or debris in lamination or clear-coats and pinholes should always be clearly defined because that’s where most discrepancies occur.
Size of Defects
A piece of dust smaller than 1 point (or 1/72 inch) in a 12-by-24-inch lamination project is not noticeable to the naked eye, but debris that is 5 or 6 points long probably would be.
When defining acceptable defect sizes, be sure to think relatively to the sizes of your parts. Most companies will define one set of quality standards that apply for all graphics supplied to them, but if your company orders different sizes, you should adjust your guidelines accordingly.
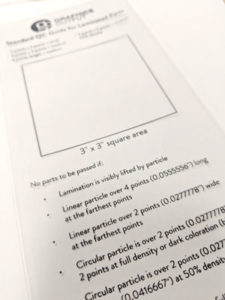
Graphics Output has developed tools to help simplify the QC process for employees, like the lamination guide above.
Number of Defects in an Area
While one small defect may be acceptable, multiple small defects in the same area might not be. A small cluster of lint can attract more attention than more individual pieces spread out across a part. For example, Graphics Output uses an internal standard of no more than four debris particles within 3 square inches for laminated parts.
Graphics Output has worked with many customers to create quality control guidelines. If you need help outlining your standards, email sales@gographicsoutput.com or call 260-748-0577.