Customers use powder coats instead of traditional wet paint for a variety of reasons. Powder coats look great, and they’re extremely durable. They’re chemically resistant and can often be more cost-effective and environmentally safe than paint.
However, it’s not always easy to adhere labels and graphics to powder coats, which include plastic additives—and it’s notoriously hard to stick anything to plastic. The three biggest hurdles for adhering a decal to a powder coating are surface energy, textured surfaces, and contoured surfaces.
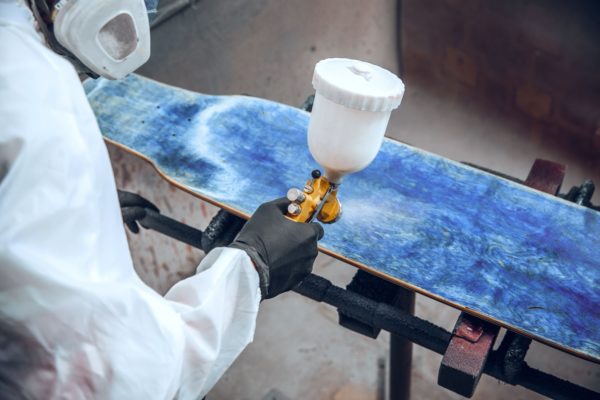
Industrial paints like this release dangerous volatile organic compounds, often called VOCs, so many companies are making the switch to non-toxic powder coats. (photo source)
Surface Energy
Pressure-sensitive adhesive bonds decals and overlays to a product. How well adhesive tacks, or sticks, to a surface is called “wetting out.” Think of water beading on a waxed car versus spilling over an unwaxed car. The more the water beads, the less it wets out, or adheres. The less the water beads, the more it wets out, or adheres. Because powder coating has a low surface energy substrate, often called LSEs, it is difficult for items to adhere to it.
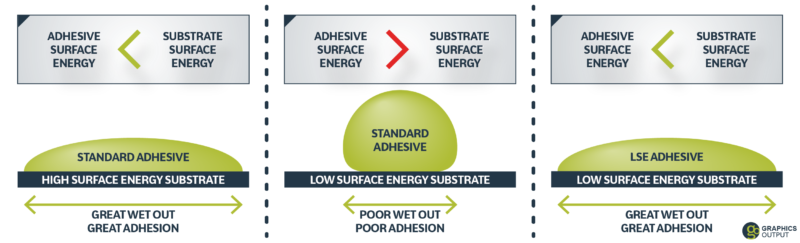
A scientific representation of “wetting out”.
Luckily, more aggressive adhesives are made specifically for low surface energy substrates, such as 3M 9472LE or Necal 9502 Adhesive Transfer Tapes. Adhesives formulated with low surface energy adhere to both LSE and HSE surfaces easily.
However, aggressive LSE adhesives can be costly. It is always a good idea to test an adhesive to assure proper bonding before making a final decision on which adhesive to use.
Textured Surfaces
Textured powder coating comes in a range of finishes, from hammered metal to fine sandpaper. Textures are popular for industrial products that need scratch resistance or a tactile element. These textures create peaks and valleys on the surface, and a label’s adhesive will meet and adhere to only the tops of the peaks. This leaves little surface area contact, weakening the adhesive bond and increasing the likelihood that decals will fall off.
The solution is to use thicker adhesives. The thickness allows the adhesive to sink into the valleys of the texture, maximizing surface area contact. Many LSE adhesives are available in a variety of thicknesses
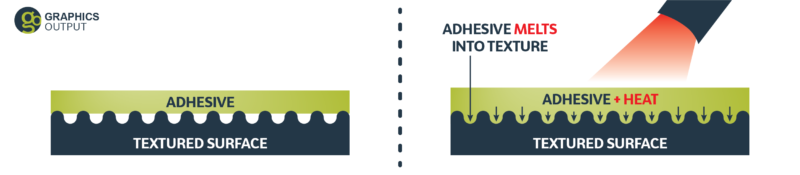
Time and heat can make it easier to spread thick adhesives, allowing for better surface area contact.
Heat can also help adhesive to ooze and flow. If you are having trouble getting a graphic to stick to a textured surface, set it out in the sun for a few hours or use a hairdryer to melt the adhesive a bit.
Extremely smooth, high-gloss powder coats can make bonding difficult since there is no texture or traction to grip to. However, adhesives designed for LSE surfaces are aggressive enough to combat the issue. Using thicker adhesives is an unnecessary expense for any smooth powder coat surfaces, regardless of finish. The lack of texture on such a smooth surface means the adhesive will sit on top of the surface, no matter how much adhesive you use. Too-thick adhesives are also more prone to oozing out from under the surface of a decal, leaving a sticky residue near the edges that dirt can cling to, a process that may eventually contaminate the adhesive and cause failure.
Contoured Surfaces
Contoured, or curved, surfaces can affect a label’s ability to adhere because rigid labels won’t be able to conform to a curved surface shape. As a result, the label will peel up to its original shape over time.

Less flexible materials like polyester don’t adhere well to complex curved surfaces.
Polyester, a common label material, is not as flexible as vinyl and is more likely to stay in its original shape. The solution to this problem is to use a material made for complex curves. Vinyl, especially cast vinyl, is extremely flexible and can conform to complex shapes with the use of a heat gun. Many standard vinyls on the market today are manufactured with LSE adhesive. LSE adhesive-backed polyesters are available, as well, but they are suitable for flat surfaces only.
The best way to prevent graphics from falling off powder coats is to use an LSE adhesive that you’ve chosen specifically for the product. If you still have questions about powder coats and need help finding the perfect build for your application, don’t hesitate to reach out to Graphics Output at sales@gographicsoutput.com or 260-748-0577.